با دقت اندازه گیری بالا، سرعت پاسخ سریع، توانایی ضد تداخل قوی، ابزار اندازه گیری دمای مداوم نوع WLX-II از فولاد مذاب دارای نظارت آنلاین زمان واقعی تغییرات دمای فولاد مذاب است، که آخرین نسل اندازه گیری دمای فولاد مذاب با دقت بالا داخلی است. تولید - محصول.با کاربرد در کارخانه های مختلف فولاد، قابلیت اطمینان و پایداری محصول به اندازه کافی تایید می شود.مطمئناً این محصول ایده آل برای جایگزینی ترموکوپل رودیوم پلاتین است.
محدوده اندازه گیری: 700-1650 ℃
عدم قطعیت اندازه گیری: ≤ ± 3℃
طول عمر لوله دما: ≥24 ساعت (لوله های دمایی با طول عمر مختلف را می توان با توجه به وضعیت سایت تولید کرد)
دمای استفاده: 0-70 ℃ (ردیاب)، 5-70 ℃ (پردازنده سیگنال)
خروجی استاندارد: 4-20mA/1-5V (مرتبط با 1450-1650℃)
نیروی محرکه خروجی: ≤400Ω (4-20mA)
دقت خروجی: 0.5
منبع تغذیه: Ac220V±10V، 50HZ
قدرت: پردازنده سیگنال 30 وات و صفحه نمایش بزرگ 25 وات.
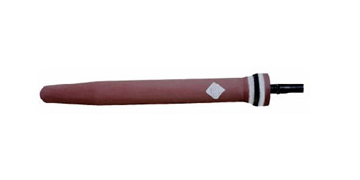

لوله دما از لوله اتصال و پوشش محافظ مقاوم در برابر آتش تشکیل شده است.پوشش محافظ مقاوم در برابر آتش از طریق لوله اتصال با آشکارساز در ارتباط است.با توجه به عمق مختلف فولاد مذاب تاندیش و خوردگی فولاد مذاب به لوله دما، طول دما دارای مشخصات 1100 میلی متر، 1000 میلی متر و 850 میلی متر است.قطر دارای مشخصات ¢85mm و ¢90mm است که می تواند با توجه به نیاز کاربران سفارشی شود.
لوله دما به طور مستقیم در فولاد مذاب وارد می شود تا دما را درک کند.عمق درج نباید کمتر از 280 میلی متر باشد.سیگنال اندازه گیری دما از سمت داخلی پایین لوله بیرونی است.زمان پاسخ ابزار اساساً برابر با انرژی زمانی است که از سمت بیرونی پایین لوله دما به سمت داخلی منتقل می شود.لوله اتصال برای اتصال بین لوله دما و آشکارساز استفاده می شود.لوله داخلی عمدتا برای از بین بردن دود داخل لوله و اطمینان از تمیزی مسیر نور است.
مورد | بدن | خط سرباره آلومینیوم منیزیم کربن | خط سرباره منیزیم |
Al2O3% | 54.8-56.2 | 61.7-62.2 | 22.7-23.3 |
SiO2% | 7.0-8.0 | ||
ZrO2% | |||
MgO% | 8.5-9.0 | 41.4-42.0 | |
FC% | 27.1-27.9 | 25.0-25.4 | 29.2-30.0 |
چگالی حجمی g/cmз | 2.46-2.53 | 2.71-2.79 | 2.48-2.52 |
تخلخل ظاهری % | 11.5-14.8 | 11.4-13.8 | 11.8-12.8 |
قدرت خرد کردن سرد MPa | 20.9-32.9 | 21.2-27.6 | 20.7-26.7 |
استحکام خمشی در دمای معمولی MPa | 20.9-32.9 | 5.4-7.3 | 5.5-8.3 |
آشکارساز از اجزای نوری، مبدل فوتوالکتریک، خط انتقال سیگنال، دوشاخه خروجی و مجرای هوای خنک کننده و غیره تشکیل شده است. ترمینال ورودی آشکارساز با لوله اتصال لوله دما وصل می شود.ترمینال خروجی از طریق پلاگین 6P به پردازنده سیگنال متصل می شود.پایانه های ورودی و خروجی توسط خط انتقال سیگنال که توسط کانال هوای خنک کننده انعطاف پذیر محافظت می شود، متصل می شوند.سیستم نوری سیگنال تشعشع مادون قرمز ارسال شده از پایین لوله دما را به مبدل فوتوالکتریک ارسال می کند، سپس مبدل فوتوالکتریک سیگنال نوری را به سیگنال الکتریکی تبدیل می کند و سپس آن را از طریق خط انتقال سیگنال به پردازنده سیگنال ارسال می کند.
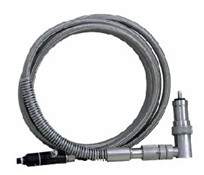
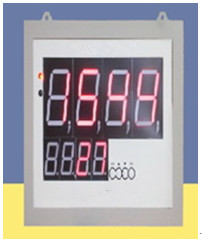
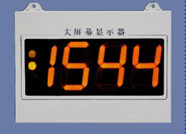
پردازنده سیگنال متشکل از ماژول قدرت، ماژول پردازش سیگنال آنالوگ، ماژول تبدیل آنالوگ دیجیتال، ماژول پردازش دیجیتال، ماژول ارتباطی و ماژول نمایش و غیره است. صفحه نمایش بزرگ از ماژول قدرت، ماژول ارتباطی و ماژول نمایش و غیره تشکیل شده است.
پردازشگر سیگنال عملکرد جبران دمای مضاعف را دارد که می تواند به طور خودکار انحراف اندازه گیری ناشی از دمای محیط سنسور و دمای کار ابزار را جبران کند.
پردازنده سیگنال ورودی سیگنال الکتریکی را توسط آشکارساز دریافت می کند.دمای فولاد مذاب اندازه گیری شده توسط ریزپردازنده بر اساس تئوری اشعه مادون قرمز محاسبه شده و بر روی صفحه نمایش داده می شود.در عین حال، داده های دمای زمان واقعی را می توان از طریق عملکرد ارتباطی روی صفحه نمایش بزرگ نشان داد.سیگنال الکتریکی می تواند به کامپیوتر کنترل اصلی برای نظارت بر فرآیند ریخته گری پیوسته در زمان واقعی ارسال شود.
1) با استفاده از این محصول می توانیم به طور مداوم و دقیق دمای فولاد مذاب تندیش و روند تغییرات را تشخیص دهیم، به موقع اقدامات لازم را برای جلوگیری از خونریزی یا گرفتگی نازل آب به دلیل دمای بالاتر یا پایین تر فولاد مذاب انجام دهیم، تلفات ناشی از خونریزی را کاهش دهیم. سوراخ های بیرون و یخ زده و زمان بیکاری به دلیل تصادفات و در نتیجه افزایش سرعت عملکرد دستگاه ریخته گری.
2) با استفاده از این محصول می توان قانون تغییر دمای فولاد مذاب تندیش را دانست.با توجه به این قانون تغییر، ما میتوانیم الزامات پارامترهای فنی معقولتری را برای فرآیند بعدی، مانند فولادسازی و پالایش، مطرح کنیم.با انجام این کار، ما نه تنها می توانیم دمای ضربه زدن را 15 تا 20 درجه سانتیگراد کاهش دهیم، بلکه از سیستم فرآیند دقیق، افزایش سطح مدیریت و دقت اندازه گیری دما نیز اطمینان حاصل می کنیم.
3) با اندازه گیری دقیق دما، این سیستم می تواند درجه حرارت فوق العاده را 5 تا 10 درجه سانتیگراد کاهش دهد.با کاهش درجه سوپرهیت، میتوانیم ناحیه کریستالی هم محور وسیعتری به دست آوریم، جداسازی مرکز ریختگی را کاهش دهیم، به طور موثر از نقص شلی، حفره انقباض و ترک جلوگیری کنیم و کیفیت فولاد را افزایش دهیم.در این بین با کاهش درجه سوپرهیت می توان سرعت ریخته گری و کیفیت فولاد را افزایش داد.روش های کاربردی ثابت می کند که این سیستم اندازه گیری دما می تواند سرعت ریخته گری را به طور متوسط 10٪ افزایش دهد.